- Typical feed: H2-rich Gas Mixture
- Capacity range: 50~200000Nm³/h
- H2 purity: Typically 99.999% by vol. (optional 99.9999% by vol.)& Meet hydrogen fuel cell standards
- H2 supply pressure: according to customer’s requirement
- Operation: Automatic, PLC controlled
- Utilities: the following Utilities are required:
- Instrument Air
- Electrical
- Nitrogen
- Electric power
Video
Methanol Cracking Hydrogen Production Technology uses methanol and water as raw materials, turn the methanol into mixed gas through catalyst and purifies the hydrogen through pressure swing adsorption (PSA) under a certain temperature and pressure.
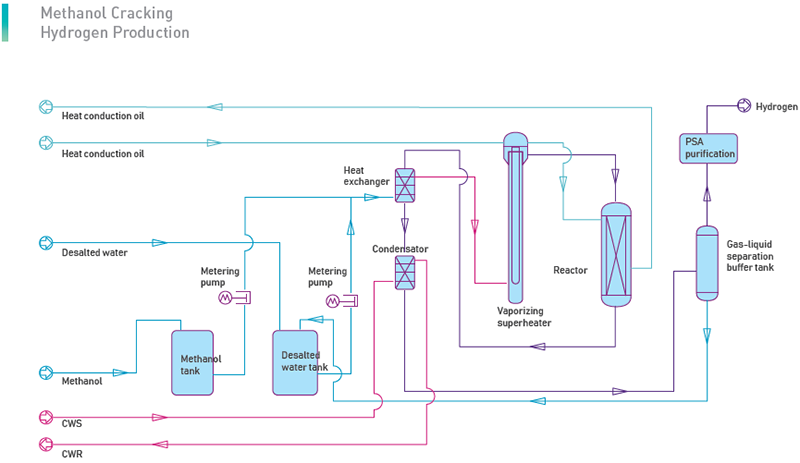
Technical Characteristics
1. High integration: the main device below 2000Nm3/h can be skidded and supplied as a whole.
2. Diversification of heating methods: catalytic oxidation heating; Self-heating flue gas circulation heating; Fuel heat conduction oil furnace heating; Electric heating heat conduction oil heating.
3. Low methanol consumption: the minimum methanol consumption of 1Nm3 hydrogen is guaranteed to be < 0.5kg. Actual operation is 0.495kg.
4. Hierarchical recovery of heat energy: maximize heat energy utilization and reduce heat supply by 2%;
(1) Methanol Cracking
Mix methanol and water in a certain proportion, pressurize, heat, vaporize and overheat the mixture material to reaches a certain temperature and pressure, then in the presence of catalyst, methanol cracking reaction and CO shifting reaction perform at the same time, and generate a gas mixture with H2, CO2 and a small amount of residual CO.
Methanol cracking is a complicated multicomponent reaction with several gas and solid chemical reactions
Major reactions:
CH3OH |
CO + H2O |
Summary reaction:
CH3OH + H2O ![]() |
The whole process is an endothermic process. The heat required for the reaction is supplied through the circulation of the heat conduction oil.
To save heat energy, the mixture gas generated in the reactormakes heat exchangewith the material mixture liquid, then condenses, and is washed in the purification tower. The mixture liquid from the condensation and washing process is separated in the purification tower. The composition of this mixture liquid is mainly water and methanol. It is sent back to the raw material tank for recycling. The qualified cracking gas then is sent to the PSA unit.
(2) PSA-H2
Pressure Swing Adsorption (PSA) is based on the physical adsorption of gas molecules on the inner surface of a specific adsorbent (porous solid material). The adsorbent is easy to adsorb high-boiling components and difficult to adsorb low-boiling components at the same pressure. The adsorption amount increase sunder high pressure and decreases under low pressure. When the feed gas passes through the adsorption bed under a certain pressure, the high-boiling impurities are selectively adsorbed and the low-boiling hydrogen which is not easily adsorbed gets out. The separation of hydrogen and impurity components is realized.
After the adsorption process, the adsorbent desorbs the absorbed impurity when reducing the pressure so that it can be regenerated to adsorb and separate impurities again.