Pressure swing adsorption oxygen production equipment (PSA oxygen production plant) is mainly composed of an air compressor, an air cooler, an air buffer tank, a switching valve, adsorption tower and an oxygen balancing tank. The PSA Oxygen Unit under the conditions of normal temperature and pressure, use the PSA special molecular sieve to selectively adsorb the nitrogen, carbon dioxide and water in the air to obtain high purity oxygen (93%±2). Since the pressure swing adsorption oxygen generator (PSA O2 generator) entered the industrialization, the technology has developed rapidly, it has strong competitiveness in the low and medium oxygen production capacity with not too high purity field because of its lower price and good performance.
Oxygen generator application field is very widely, including electric arc furnace steelmaking for metallurgy industry, blast furnace ironmaking oxygen enrichment, oxygen-enriched combustion shaft furnace lead smelting non-ferrous smelting, copper smelting, zinc smelting, aluminum smelting, oxygen enrichment of various furnaces. It also can be sued in environmental protection water treatment, wastewater treatment, pulp bleaching, sewage biochemical treatment, various oxidation reactions in chemical industry, ozone production, coal gasification, other industrial fermentation, cutting, glass furnaces, waste incineration, oxygen therapy, sports and health care, freshwater aquaculture etc.
PSA oxygen plant has the following characteristics:
1. The PSA oxygen generation plant unit is simple, the power equipment is only air compressor and cooler.
2. The molecular sieve requirements are relatively low, the same O2 Plant using the amount of molecular sieve is less.
3. The Oxygen Machine is small, so its cost is relatively low.
4. The degree of automation of the whole PSA oxygen system is relatively low, air compressor, freeze dryer/condenser can be separated from the oxygen generator to start and stop control, and also can be linked control.
5. The O2 generator reasonable design of gas distribution structure, unique molecular sieve filling process and automatic compression compensation system makes normal service life of the adsorbent can reach more than 10 years.
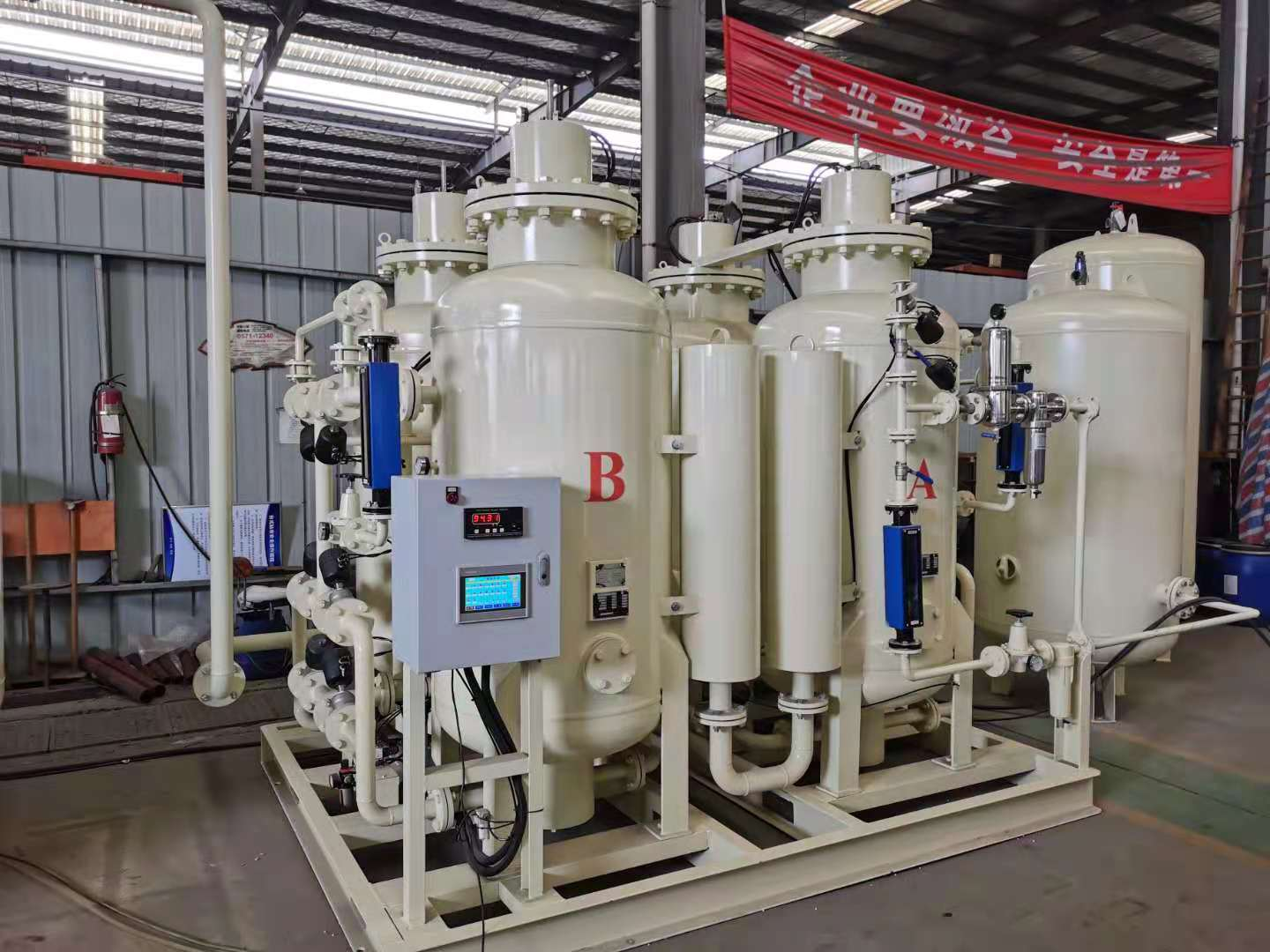
Post time: Feb-27-2024